In the world of manufacturing, few processes are as versatile and widely used as blow molding. From everyday items like water bottles and shampoo containers to automotive fuel tanks and industrial drums, blow molding plays a pivotal role in creating hollow plastic products. But how does this fascinating process work? Let’s break down the basic principles behind blow molding and explore why it’s a cornerstone of modern production.
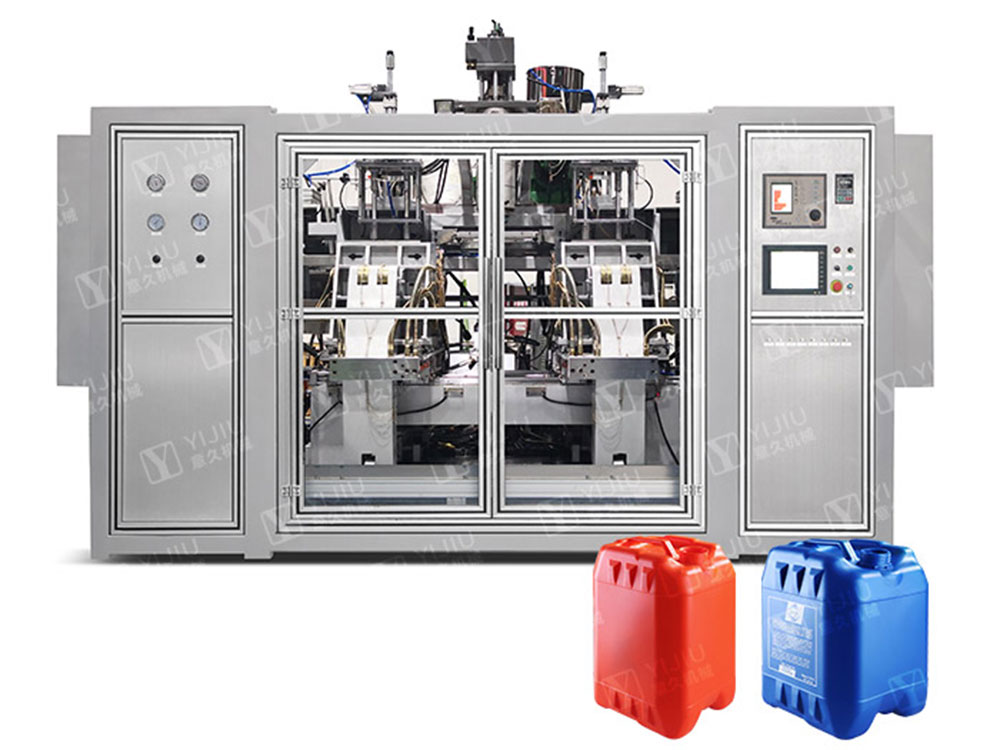
What is Blow Molding?
Blow molding is a manufacturing technique used to produce hollow, lightweight plastic parts by inflating a heated plastic tube (called a parison or preform) inside a mold. The process mimics blowing up a balloon: air pressure expands the softened plastic to conform to the shape of the mold, resulting in a seamless, hollow product.
The Three Key Stages of Blow Molding
While variations exist (more on that later), the core principle involves three fundamental steps:
1.Melting and Forming the Parison
– Plastic resin (typically polyethylene, PET, or PVC) is melted and extruded or injection-molded into a tubular shape called a parison. This tube hangs vertically and is clamped at one end.
2.Inflation with Compressed Air
– The parison is enclosed within a two-part mold. High-pressure air (20–150 psi) is injected into the tube, forcing it to expand outward until it matches the mold’s contours.
3.Cooling and Ejection
– Once the plastic cools and solidifies, the mold opens, and the finished product is ejected. Excess material (called flash) is trimmed, leaving a smooth, hollow part.
Types of Blow Molding
1.Extrusion Blow Molding (EBM)
– The most common method. A continuous parison is extruded, clamped into a mold, and inflated. Ideal for high-volume production of bottles, containers, and large industrial parts.
2.Injection Blow Molding (IBM)
– A preform is first injection-molded, then transferred to a blow mold for inflation. Offers precise control over wall thickness and is often used for small, complex shapes like medical bottles.
3.Stretch Blow Molding (SBM)
– Combines stretching and blowing to create biaxially oriented products (e.g., PET soda bottles). The preform is stretched longitudinally before air expands it radially, enhancing strength and clarity.
Why Blow Molding Matters
This process’s popularity stems from its efficiency, scalability, and design flexibility:
– Cost-Effective: Low material waste and high-speed production make it ideal for mass manufacturing.
– Lightweight & Durable: Produces strong, thin-walled parts ideal for packaging and transportation.
– Complex Geometries: Enables intricate shapes and uniform wall thickness, even for large items.
Blow molding is a perfect marriage of simplicity and engineering sophistication. By harnessing air pressure and heat, it transforms raw plastic into the functional, lightweight products we rely on daily. As technology evolves, this process will continue to shape the future of manufacturing—one hollow part at a time.